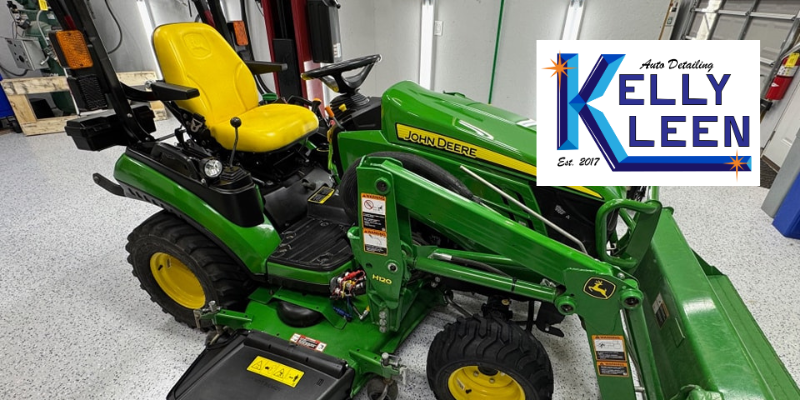
Top 10 Benefits of Investing in Construction and Farm Equipment Coatings: Maximizing Efficiency and Lifespan
In industries like construction and farming, equipment is more than just a set of tools—it’s a lifeline. From excavators and bulldozers to tractors and combine harvesters, these heavy-duty machines keep projects on schedule and feed our communities. But frequent exposure to dirt, moisture, harsh chemicals, and extreme weather can take a toll on such equipment, often leading to premature wear, breakdowns, and costly repairs.
That’s where specialized protective coatings come in. By applying industrial-grade coatings (often ceramic-based or polymer-based), you create a robust shield that safeguards your heavy machinery against corrosion, abrasions, and everyday wear. If you’ve ever wondered how to extend the lifespan of your farm or construction equipment—and save money over the long haul—this guide is for you. Below, we explore the top ten benefits of investing in protective coatings and how professional services, like those offered by Kelly Kleen Auto Detailing, can dramatically improve your bottom line.
Table of Contents
- Why Protective Coatings Matter
- Benefit #1: Corrosion and Rust Prevention
- Benefit #2: Extended Equipment Lifespan
- Benefit #3: Reduced Maintenance Costs
- Benefit #4: Time Savings
- Benefit #5: Enhanced Resale Value
- Benefit #6: Improved Fuel Efficiency
- Benefit #7: Enhanced Safety
- Benefit #8: Aesthetic Appeal and Branding
- Benefit #9: Positive Environmental Impact
- Benefit #10: Versatility and Custom Solutions
- Choosing the Right Coating Service Provider
- Tips for Maximizing Coating Performance
- Conclusion
Why Protective Coatings Matter
In both the construction and agricultural sectors, your machinery is often your largest capital investment. Protecting that investment from the elements and daily wear is crucial for staying competitive and profitable. Protective coatings can:
- Form a Defensive Shield: Guard against rust, moisture, chemicals, and ultraviolet (UV) damage.
- Simplify Maintenance: Make surfaces easier to clean and reduce the need for harsh chemicals.
- Increase Efficiency: Minimize downtime and operational delays caused by preventable repairs.
- Boost Longevity: Extend the usable life of expensive equipment.
You can opt for Ceramic Coatings, Polyurethane Coatings, Epoxy-based Coatings, or other specialized blends designed for heavy-duty applications. Each type has its own set of benefits, such as enhanced UV resistance, scratch resistance, or chemical resilience.
Professional services like Kelly Kleen’s Construction Equipment Coatings or Farm Equipment Coatings take these solutions a step further by offering experienced technicians and premium-grade materials, ensuring your coatings are applied correctly and effectively.
Benefit #1: Corrosion and Rust Prevention
The Enemy Within: Corrosion
Heavy equipment is constantly exposed to moisture, whether it’s through rain, snow, high humidity, or even daily washing. Add in the possibility of salt (in winter road work) or fertilizers (in farming), and corrosion becomes a very real, ever-present threat. Rust can weaken metal components, eat away at crucial parts, and eventually lead to structural failures.
How Coatings Help
- Barrier Protection: A proper coating forms a physical barrier that inhibits water, salt, and oxygen from penetrating to the metal substrate.
- Chemical Resistance: Coatings with high chemical resistance protect surfaces from acids, alkalines, and other corrosive substances you might encounter on a job site or in the fields.
For operators in the agricultural space, fertilizer and pesticide runoff can wreak havoc on machinery. By investing in specialized farm equipment coatings, you significantly reduce the odds of corrosion cutting your tractor’s life short.
Benefit #2: Extended Equipment Lifespan
One of the clearest returns on investment (ROI) with protective coatings is how much they prolong the overall lifespan of machinery.
Key Factors
- Reduced Abrasive Wear: Construction sites are full of abrasive elements—dirt, rocks, debris—that grind against equipment surfaces. Coatings add a protective layer to reduce direct impact.
- Less UV Damage: Prolonged exposure to sunlight can degrade paint and weaken certain materials. UV-resistant coatings slow this deterioration.
- Impact Resistance: High-grade coatings can absorb some level of shock and vibration, reducing the chance of dents, chips, and micro-fractures over time.
Money Saved in the Long Run
Replacing large machines like excavators or combine harvesters is a significant capital expense. By extending each machine’s functional life by years, you not only defer that major purchase but also gain a competitive edge by lowering overhead costs.
Benefit #3: Reduced Maintenance Costs
Maintaining heavy equipment can be expensive, from routine tune-ups to unexpected part replacements. Protective coatings directly reduce these expenses in several ways:
- Ease of Cleaning: Equipment coated with slick, non-porous surfaces is easier to wash. Mud, grease, and debris don’t cling as stubbornly, meaning you use fewer cleaning products and less water.
- Fewer Part Replacements: Rusted or corroded parts often need replacing sooner than anticipated. A coating prevents or slows rust, thus reducing the frequency of new parts.
- Lower Labor Costs: Because maintenance is simpler, you need less labor time for cleaning, inspections, and repairs. Over the long haul, this can amount to substantial savings.
Consider how many hours your crew or technicians spend on cleaning and upkeep. If that time is halved—courtesy of an easily cleaned protective surface—you’ll see the financial benefits accumulate quickly.
Benefit #4: Time Savings
Whether you’re working on a tight construction deadline or managing a busy planting and harvesting schedule, time is one of your most valuable resources. Equipment coatings cut down on the time spent on non-productive tasks:
- Faster Wash-Downs: Power-washing mud and debris off coated surfaces takes a fraction of the time compared to uncoated metal.
- Quick Visual Inspections: A well-coated machine has fewer hidden rust spots or corrosion-prone areas, making it easier to spot any potential issues early.
- Reduced Downtime: Since coated surfaces experience fewer breakdowns from rust or minor surface damage, your equipment stays in operation longer.
For large-scale operations with multiple pieces of machinery, these time savings add up dramatically. Every hour saved in maintenance is an hour that can be spent moving earth or harvesting crops, directly impacting your revenue.
Benefit #5: Enhanced Resale Value
Heavy machinery often retains a portion of its value well after initial purchase—assuming it’s been maintained properly. When you eventually decide to upgrade, having equipment that looks and functions like new gives you a stronger position in the resale market.
Coatings as an Investment
- Better Appearance: A well-maintained, glossy appearance suggests to prospective buyers that the machine has been cared for.
- Proof of Care: Providing documentation that the equipment was professionally coated reassures buyers and can justify a higher asking price.
- Long-Term Protection: Buyers are willing to pay a premium for equipment that won’t immediately require expensive repairs or further protective measures.
Whether selling at auction or privately, a coated piece of machinery often commands more attention—and higher bids—than one that shows visible signs of wear or rust.
Benefit #6: Improved Fuel Efficiency
This might not be the first benefit you think of, but over the lifetime of your equipment, it can be significant. Drag and friction—no matter how small—can affect the energy required to operate machinery. While this is more common in the trucking or automotive realm, the principle carries over to heavy equipment.
- Less Dirt and Grime Build-Up: A slick surface reduces drag and ensures that moving parts aren’t weighed down by caked-on mud or other materials.
- Optimized Engine Performance: Indirectly, preventing rust and internal contamination through sealing can help components run smoothly, thus using fuel more efficiently.
It’s not a dramatic boost—no protective coating can magically turn a gas-guzzling excavator into a Prius—but any incremental gain in fuel efficiency, spread across dozens of machines over years, can add up to substantial cost savings.
Benefit #7: Enhanced Safety
In heavy industries, safety is paramount. Protective coatings can play a surprisingly vital role here too:
- Structural Integrity: Coatings help prevent corrosion that compromises the structural soundness of critical components—an especially pressing concern in cranes, lifts, and other machinery carrying heavy loads.
- Reduced Slippage: Some specialized coatings have anti-slip properties, beneficial for surfaces where operators or maintenance crew frequently step.
- Clear Visibility of Damage: Coated surfaces often make it easier to spot any cracks or issues that do arise. Early detection of potential failures can prevent catastrophic accidents.
Workers who feel secure operating well-maintained machines are less likely to experience accidents, fostering a safer work environment and reducing the risk of costly downtime or liability claims.
Benefit #8: Aesthetic Appeal and Branding
While aesthetics may not be your top priority, the appearance of your equipment can influence how clients, partners, and even regulators perceive your operation.
- Professional Image: Crisp, well-maintained machinery gives the impression of an organized, detail-oriented business. This could be a deciding factor when bidding on high-profile construction jobs or attracting lucrative contracts.
- Brand Visibility: Many coatings can be tinted or matched to your company’s color scheme. Adding custom decals over a pristine, coated surface ensures that your equipment effectively represents your brand wherever it goes.
- Employee Pride: Operators and crew members are often more motivated to maintain and respect equipment that looks professionally cared for, contributing to a culture of diligence and responsibility.
In competitive markets, the little details (like pristine, branded machinery) can set you apart from competitors who let their equipment fall into a state of disrepair.
Benefit #9: Positive Environmental Impact
Companies across all industries are looking for ways to operate more sustainably, and protective coatings can help in multiple ways:
- Fewer Harsh Chemicals: Because coated surfaces are easier to clean, you typically need less detergent or solvents to remove dirt and grime. This reduces chemical runoff and potential soil or water contamination.
- Longer Equipment Life: Extending the lifespan of machinery reduces waste, conserves resources, and lowers your carbon footprint by minimizing the production and disposal of new equipment.
- Efficient Upkeep: Lower maintenance needs translate to fewer service trips, less idle time, and potentially reduced fuel consumption, all of which reduce greenhouse gas emissions.
By taking steps to protect and maintain your equipment, you’re also playing a part in fostering an eco-friendly operation—something that can be significant in industries where environmental impact is heavily scrutinized.
Benefit #10: Versatility and Custom Solutions
Not all coatings are created equal. The beauty of modern protective solutions is that they’re highly adaptable. You can find products that cater specifically to:
- Chemical Resistance: Ideal for agriculture, where fertilizers, pesticides, and other corrosive agents are prevalent.
- High-Temperature Resistance: Crucial for construction equipment used near hot surfaces or in intense climates.
- Abrasion Resistance: Perfect for environments where equipment frequently encounters stones, gravel, or other abrasive materials.
- Hydrophobicity: Coatings that repel water can be beneficial in wet or high-humidity regions.
Whether you’re running a small family farm or coordinating a large-scale construction fleet, you can tailor the type of coating to your unique operational needs. Professional application services will assess your equipment and specific use cases, recommending a specialized solution for maximum protection and ROI.
Choosing the Right Coating Service Provider
Selecting the right service provider is just as important as choosing the right coating. Look for these key qualities:
- Industry Experience: Providers like Kelly Kleen have deep knowledge of both construction and agricultural machinery. They understand the unique stressors each environment brings.
- High-Quality Materials: Always inquire about the brands and types of coatings used. Certifications and warranties can indicate superior-quality products.
- Preparation Process: Proper surface preparation (cleaning, degreasing, roughing up the surface for adhesion) is crucial for coating effectiveness. Make sure the provider has a rigorous prep routine.
- Post-Application Support: A good partner will offer guidance on aftercare, maintenance schedules, and how to spot potential issues early.
Don’t hesitate to ask for references or examples of previously coated equipment to gauge the provider’s track record.
Tips for Maximizing Coating Performance
While investing in a protective coating is a big step, you’ll want to ensure you get the most out of it:
- Regular Inspections: Even with a coating, rust or damage can occur over time. Inspect your equipment monthly for signs of wear or chipping.
- Proper Cleaning: Although coatings make cleaning easier, it’s still essential to rinse off corrosive agents as soon as possible. Avoid letting mud or chemicals bake onto the surface.
- Touch-Up Repairs: Small chips can expose metal beneath the coating. Promptly address any areas of concern by applying touch-up products recommended by your coating provider.
- Follow Manufacturer Guidelines: Each coating has specific cure times and maintenance requirements. Adhering to these guidelines extends the life of your protective layer.
By combining diligent care with professional-grade coatings, you’ll create a potent defense against the harsh realities of construction sites and farm fields alike.
Conclusion
From corrosion resistance and safety enhancements to environmental benefits and better resale value, protective coatings are a game-changer for construction and farm equipment. They help you focus on what matters most—getting the job done on time and on budget—while preserving the longevity and performance of your most critical assets.
Whether you manage a fleet of excavators or maintain a single tractor on a small farm, investing in high-quality coatings can streamline maintenance, reduce costs, and keep your machinery running smoothly for years to come. In competitive industries, every edge counts, and this is one investment that consistently delivers returns.
If you’re ready to explore the possibilities of a professional coating application, consider partnering with an experienced provider like Kelly Kleen Auto Detailing. From Construction Equipment Coatings to Farm Equipment Coatings, their specialized knowledge and state-of-the-art techniques ensure your machines receive the protection they deserve.
Invest in coatings now, and watch as you maximize efficiency, minimize downtime, and secure a longer, more productive future for your valuable equipment.